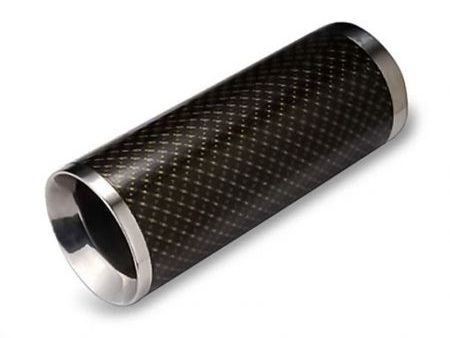
Carbon Fiber Parts Manufacturing
Superior Carbon Fiber Cloth with Best Manufacturing Quality
Pan Taiwan manufactures a broad range of high-performance carbon fiber parts for both automotive and industrial applications. We take pride in our advanced manufacturing processes, utilizing high-quality carbon fiber cloth from TORAY and Mitsubishi to produce parts with excellent mechanical strength and consistently clear carbon fiber patterns. From hand lay-up, pultrusion, hot press, filament winding, to compression molding, we suggest the most suitable process for your design.
We specialize in customized carbon fiber parts, including but not limited to:
Strut bars
Hydrofoil parts
Battery covers
Bike frames
Carbon fenders
Rear mirror covers
Carbon pipes
End caps of carbon exhaust pipes
We make customized carbon fiber parts
Our team of professionals, including R&D and QC specialists, ensures that the quality and specifications of our products meet the highest standards. Certified to ISO 9001, we adhere to strict protocols to produce top-quality carbon fiber materials. With our extensive experience, we are confident in meeting your technical requirements and deadlines.
The advantages of carbon fiber parts include anti-corrosion properties, a smaller coefficient of thermal expansion, shock absorbance, and significantly lighter weight compared to metal parts. We understand that the multiple options for carbon fiber manufacturing processes can be confusing, but we will select the most suitable method for your parts. In addition to 3K, 12K, and UD finishes, we also offer dye sublimation and cloth implant finishes.
Allow us to be your best partner in carbon fiber parts manufacturing. For further information on the most suitable process for your products, feel free to contact us.
Roll Wrapping
Carbon fiber tube in Pan Taiwan are made by roll wrapping, this manufacturing process is typically...
DetailsFilament Winding
Thanks to the characteristic of the filament winding, Pan Taiwan(OEM) can not only manufacture...
DetailsPultrusion
If you are looking for a supplier for high quality carbon fiber parts in straight shape, you are looking...
DetailsCompression Molding
There are many fabrication processes to create carbon fiber parts, here at Pai Taiwan(OEM),...
DetailsHand Lay-up Process
Pan Taiwan provides custom carbon fiber manufacturing process - hand lay-up process. Hand lay-up...
DetailsVacuum Bagging
Pan Taiwan provides custom carbon fiber parts made by vacuum bagging. The mold cost is lower...
DetailsCarbon Fiber Parts Manufacturing Manufacturer | Pan Taiwan
Located in Taiwan since 1977, Pan Taiwan Enterprise Co., Ltd. has been a manufacturing process services provider. Our main manufacturing process services include, Carbon Fiber Parts Manufacturing, tactical bags manufacturing, custom bike frames, custom carbon fiber products, multi-tools, custom plastic injection parts, product assembly, reverse engineering, investment casting parts, machined parts, sheet metal stamping, bike caps, which have ISO 9000 and ISO 13485 quality assurance certifications.
Pan Taiwan with certified ISO 9001 provides manufacturing services and total solutions for anyone who has any custom parts in need we have sophisticated experiences to partner with a wide range of manufacturers from Plastic Injection, Die Casting, Forging, CNC machining, Tactical Bags, EDC pouches or standard bicycle and outdoor activity parts for nearly 50 years, so we will act as your eyes and ears for any project you have with us. We don't just supply bicycle parts, accessories, and carabiners in multiple applications. We also offer OEM and ODM services to make your idea come true. The manufacturing processes we're good at are plastic injection, sheet metal stamping, investment casting, MIM and many more.
Pan Taiwan has been offering customers manufacturing process services, both with advanced technology and 50 years of experience, Pan Taiwan ensures each customer's demands are met.